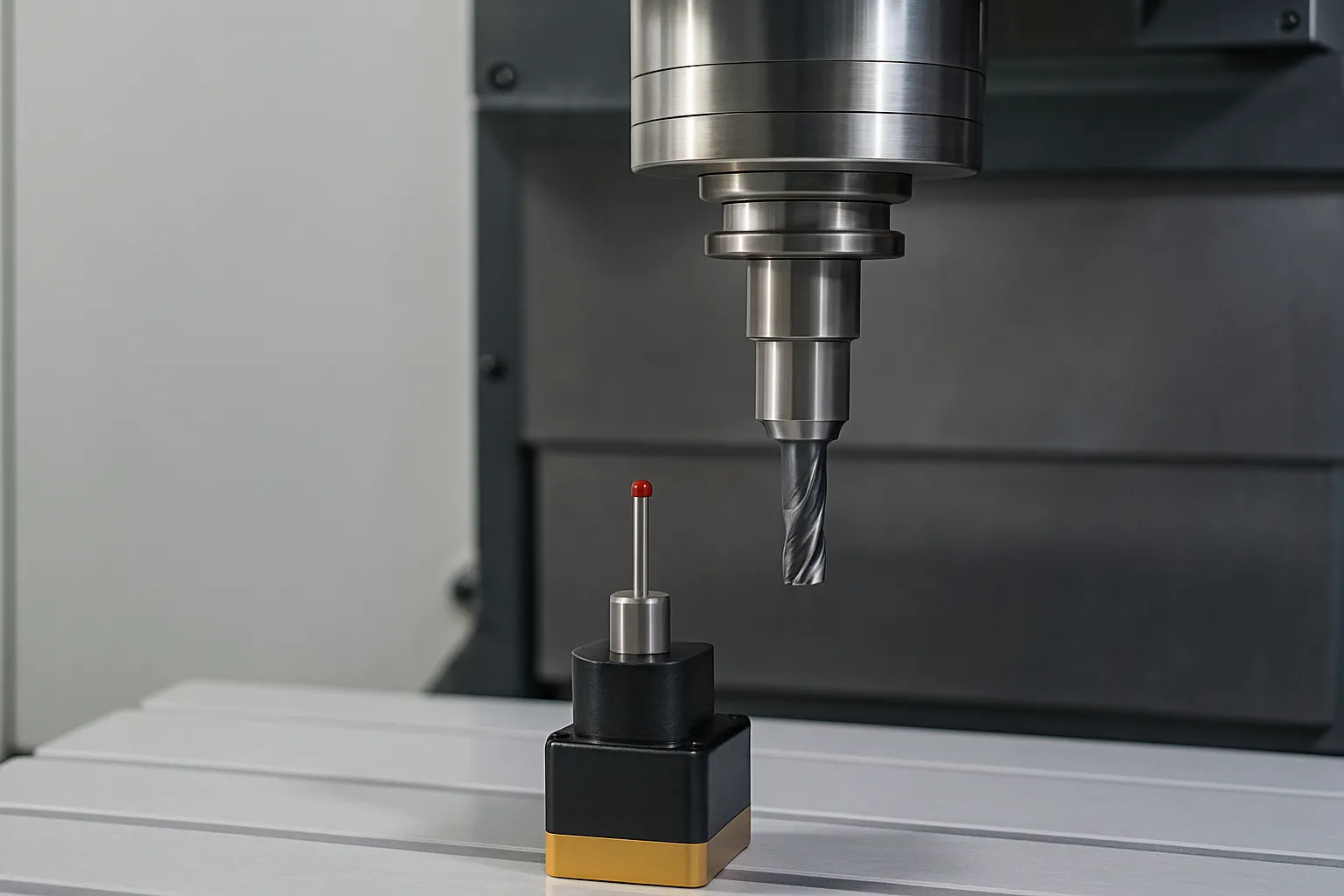
Introduction
In the world of CNC machining, precision is everything. One of the most critical components for ensuring accuracy and efficiency is the tool setting gauge. However, with so many options available, selecting the right gauge can be challenging. In this article, we’ll guide you through the key factors to consider when choosing a tool setting gauge for your CNC machine.
1. Understand the Purpose of a Tool Setting Gauge
A tool setting gauge, also known as a tool presetter, helps you measure the precise length and diameter of cutting tools before machining. By setting tools correctly, you reduce setup time, minimize errors, and improve the overall machining quality.
2. Know Your CNC Machine Specifications
Before purchasing, check your machine’s compatibility:
- Spindle type and speed
- Tool holder style (BT, HSK, CAT, etc.)
- Machine control system (FANUC, SIEMENS, MITSUBISHI, etc.) Choosing a gauge that matches your machine specifications ensures seamless integration and accurate readings.
3. Select Between Contact and Non-Contact Types
There are two main types of tool setting gauges:
- Contact Type: The tool physically touches a sensor for measurement. It’s durable and cost-effective.
- Non-Contact Type: Uses lasers or optical sensors for measurement. It offers higher precision but usually comes at a higher price.
4. Check the Durability and Build Quality
Since the gauge will be exposed to cutting fluids, metal chips, and vibrations, it must be:
- Water-resistant
- Dustproof
- Vibration-resistant Look for gauges with IP65 or higher protection ratings and robust construction materials like stainless steel or hardened aluminum.
5. Consider the Installation and Calibration
- Ease of Installation: Some gauges require professional installation, while others are plug-and-play.
- Calibration Requirements: Check if the gauge needs frequent recalibration or offers automatic calibration functions.
Choosing a user-friendly gauge can save you significant time and maintenance costs in the long run.
6. Budget vs. Performance
Higher-end gauges come with additional features like wireless data transmission, automatic tool breakage detection, and compatibility with various CNC software. Evaluate your production needs before investing in premium models.
Conclusion
Choosing the right tool setting gauge is an investment in your CNC machining precision and efficiency. By understanding your machine’s requirements, selecting the appropriate type, and prioritizing durability and ease of use, you can significantly enhance your production capabilities. Always consult with your tool setting gauge supplier to ensure you pick the best option for your specific applications.